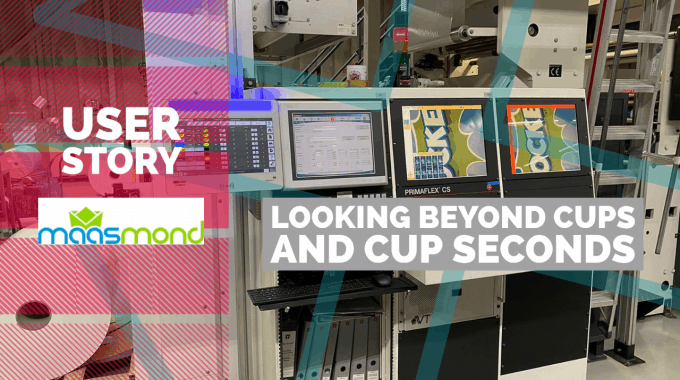
Maasmond BV alcança precisão e consistência de cores de impressão com Rheonics Sistema SRV e RPS InkSight
DETALHES
Aplicação
Controle de qualidade de impressão em unidades de impressão flexográfica e laminação.
Desafio
- As medições da viscosidade do copo não têm a precisão para combater problemas de impressão relacionados à viscosidade dentro da impressora com simplicidade
- A calibração manual de viscosímetros com um copo ou algum tipo de referência é entediante e ineficiente
Solução
- A Rheonics O viscosímetro SRV fornece medições ultraestáveis, repetíveis e precisas sem a necessidade de qualquer recalibração
- Além do controle de qualidade de impressão superior, o sensor fornece muitas informações sobre o comportamento das tintas, transformando as operações de controle de qualidade em um nível totalmente novo.
- Com o RPS InkSight, o controle de qualidade de impressão totalmente automático é possível com extrema simplicidade e intuitividade
USUÁRIO
Empresa: Maasmond BV
Locação: Oostvoorne, Holanda
Pessoa de contato: Bert Verweel, Diretor e Proprietário
Sobre a empresa
Maasmond é uma empresa familiar (fundada em 1969) com 50 anos de experiência na conversão de papel e plásticos. Para a conversão de embalagens e rótulos alimentícios e não alimentícios, temos uma ampla gama de modernas impressoras flexográficas de banda larga e estreita (tintas à base de UV e solvente), laminação (adesivos à base de água e solvente), corte, corte e vinco e perfuração máquinas. A Maasmond produz uma ampla variedade de rótulos de alta qualidade e embalagens flexíveis que atendem aos mais altos padrões de embalagem de alimentos.
- Você poderia nos contar sobre sua empresa e suas operações? Há quanto tempo sua empresa tem experiência?
Resposta:
Maasmond é uma empresa familiar (fundada em 1969) com 50 anos de experiência na conversão de papel e plásticos. Para a conversão de embalagens e rótulos alimentícios e não alimentícios, temos uma ampla gama de modernas impressoras flexográficas de banda larga e estreita (tintas à base de UV e solvente), laminação (adesivos à base de água e solvente), corte, corte e vinco e perfuração máquinas. A Maasmond produz uma ampla variedade de rótulos de alta qualidade e embalagens flexíveis que atendem aos mais altos padrões de embalagem de alimentos.
- Como e quando você soube Rheonics Solução de impressão (RPS)?
Resposta:
Eu estava procurando sensores de viscosidade de reposição há alguns anos. Em dezembro de 2017, me deparei com o site da Rheonics e o que me atraiu imediatamente foi a compacidade, robustez (resistir a altas pressões e ambientes abrasivos) e precisão. Em janeiro de 2018, durante 2 dias testamos alguns sensores e percebemos imediatamente que este sensor é fenomenal em termos de precisão e estabilidade. Durante esses testes, variamos a quantidade de solvente e até mesmo a influência do retardador e do acelerador pôde ser registrada.
- Antes de implantar o RPS, quais foram os principais desafios que você enfrentou e precisava resolver?
Resposta:
A desvantagem de todos os sensores existentes no mercado é que eles sempre precisam ser calibrados manualmente com um copo para ter algum tipo de referência. Muitas vezes, ao preparar e ajustar uma cor, a primeira questão era se a viscosidade estava correta e se o sensor estava calibrado. Naquela época, a viscosidade das cores variava muito (valores divergentes devido à não calibração), enquanto agora trabalhamos com valores fixos e, portanto, somos muito mais rápidos na cor. A dosagem de solventes foi grosseira causando um desvio de viscosidade considerável.
- Você conseguiu resolver os desafios?
Resposta:
O maior desafio foi se acostumar com a unidade mPa.s, pois já trabalhamos com a “unidade” Din Cup há décadas. No início convertemos mPa.s em segundos Cup, mas logo decidimos que isso é um absurdo, temos um sensor que funciona com a unidade correta com valores repetíveis, então vamos usá-lo. O sensor também nos deu muito conhecimento extra sobre o comportamento das tintas, até ousamos dizer mais do que os fornecedores de tinta sabem.
- Que valor esse sistema trouxe em termos de qualidade de impressão, produtividade, economia e ROI?
Resposta:
Apenas por causa da precisão do sensor e do controle, a viscosidade é mantida com extrema precisão durante a produção, os valores dE tornaram-se mais constantes e precisos. Por exemplo: para repetir o pedido, usamos tinta residual e dosamos a quantidade de tinta que faltava e podemos realmente manter o mesmo valor de viscosidade da primeira vez que a cor foi impressa. Isso dá muita confiança às impressoras. Devido ao conhecimento adquirido e ao comportamento da tinta nos substratos em que imprimimos, sabemos quais valores de viscosidade devem ser respeitados, o que economiza muito tempo, reduz desperdícios e desperdícios (devido a testes manuais e configurações).
A maior confiança no controle sobre a qualidade de impressão com o RPS nos permitiu assumir margens mais altas e trabalhos de qualidade mais altos onde os proprietários das marcas têm especificações de cores muito rígidas. Temos um cliente e um concorrente que também fornece foil, seus valores dE2000 estão entre 4-5, os nossos abaixo de 2. Nosso preço de venda é superior ao do concorrente e neste caso o preço determina a qualidade. Sempre buscamos valores baixos de dE2000 para manter o nível de qualidade o mais alto possível e dificultar a competição. O sistema possui outros recursos avançados, como a capacidade de detectar o entupimento / entupimento da linha de impressão. Essas funcionalidades inteligentes do RPS InkSight estendem a vida útil de nossas impressoras em pelo menos 2 anos.
As funcionalidades do sistema se estendem à análise de falhas e solução de problemas eficazes. Na semana passada, observamos 'fantasmas' em nossos trabalhos de impressão - o que é causado principalmente pela falha do anilox em fornecer consistentemente tinta suficiente durante todo o processo de impressão. Resolvemos esse problema adicionando acetato de etila (garante que a tinta se dissolva bem e seque mais rápido) à tinta em várias etapas. A viscosidade desceu de 45 para 32 mPa.s. A viscosidade em mPa.s caiu drasticamente, no entanto, se fosse medida com um copo, nenhuma grande alteração poderia ser medida, talvez 0,5-1 s. As xícaras não têm a precisão para combater efetivamente esses problemas dentro da impressora com a simplicidade e a intuitividade que o sistema RPS capacita nossos operadores.
O governo holandês exige o acompanhamento e a prova de quantas emissões de solventes Maasmond tem, para as quais devemos fazer medições de emissões e ter uma administração de equilíbrio de solventes. Vimos nos últimos 2 anos que o consumo de solventes diminui, principalmente em 2020 vemos uma diminuição enorme. Naquele ano, o laminador foi equipado com o controle de viscosidade do Rheonics, o que resultou em uma redução de 21% de acetato de etila.
- Foi fácil / difícil comissionar o RPS em seu processo? Quais são seus comentários sobre o funcionamento e usabilidade do sistema e software? Foi fácil para seus operadores entender e se adaptar a isso?
Resposta:
Na verdade, o software e o hardware são plug and play.
Uma característica fundamental do Rheonics O viscosímetro SRV é sua facilidade de integração em linha, o que significa menores custos e esforços de instalação. O SRV não faz exigências quanto à forma como é instalado. Devido às dimensões compactas do sensor, ele quase não ocupa espaço. Não gera nenhuma resistência na linha de alimentação e também mantém o sensor sempre limpo. As vibrações causadas pelas pulsações da bomba ou da máquina não influenciam o sensor, o que representa uma grande vantagem competitiva em relação a outros sistemas similares. Por exemplo, com o inkspec, os sensores devem ser configurados de maneira isolada, caso contrário, as vibrações (mesmo os sensores influenciam mutuamente a medição de cada sensor individual) são claramente visíveis nas máquinas onde os sensores inkspec são usados. Isso ocupa muito espaço e torna a instalação cara.
No ano passado, instalamos um segundo RPS no laminador, os operadores precisavam apenas de uma breve explicação. Os operadores estavam acostumados a pensar em segundos e, uma vez acostumados com a nova unidade, eles sabem exatamente o que estão fazendo. As viscosidades dos adesivos de 2 componentes são baixas e podem se desviar muito rapidamente devido à alta taxa de evaporação do acetato de etila. O software RPS InkSight mostra em tempo real qual é a viscosidade e o controle fornece compensação para a evaporação real. Também aqui se aplica que, para diferentes substratos, certas viscosidades devem ser usadas para o adesivo e isso agora é perfeitamente possível. O que me surpreendeu é que os adesivos são preparados com mais precisão, pelo menos na quantidade de acetato de etila que tem que ser adicionada à receita. O software mostra imediatamente quando muito ou pouco está sendo dosado, o que não acontecia antes. Além disso, durante a operação, quando o adesivo novo é adicionado ao balde, o operador vê o que acontece e tornou-se um desafio preparar o adesivo da forma mais precisa possível.
- Existe alguma coisa sobre a tecnologia do Rheonics soluções que você gostaria de destacar especificamente? Qual é o desempenho preciso e confiável dessas soluções dentro da impressora em termos de metas de processo?
Resposta:
Ao comprar novos sensores, meu objetivo era ter sensores precisos e compactos com pouca manutenção. Em termos de precisão e confiabilidade, o sensor e o controle excederam nossas expectativas / objetivos e levaram a melhorias na qualidade, eficiência e automação das cores. Depois de ter avaliado, analisado e testado diferentes soluções e tecnologias para gerenciamento de qualidade de impressão, acho que RPS é uma adição extremamente valiosa para nossa impressora - torna o controle da variável mais importante - 'viscosidade da tinta' super fácil, intuitivo e revolucionário em termos de precisão. Ele define uma nova referência em termos de precisão. O RPS é pelo menos 10-15 vezes mais preciso do que outros controles de viscosidade de tinta líderes existentes no mercado.
Imprimimos em uma diversidade bastante grande de folhas e papel, onde diferentes viscosidades devem ser manipuladas e com a experiência que temos agora nos diz quanto uma tinta deve ser diluída para uma determinada intensidade de cor. Freqüentemente, usamos um certo que é usado para imprimir em diferentes substratos em que diferentes viscosidades devem ser usadas, por exemplo, imprimir em certa cor em papel (alta viscosidade é necessária) e esta mesma cor é usada para imprimir em folha (relativa baixa viscosidade ) Registramos para cada pedido, por cor, a viscosidade e qual cilindro anilox foi usado, então sabemos exatamente qual viscosidade manusear para ter a densidade de cor correta resultando em um tempo de configuração mais rápido.
Outra vantagem prática com RPS é que quantidades muito pequenas de solvente são dosadas durante o controle de viscosidade para compensar a evaporação real. A maioria dos outros sistemas requer grandes quantidades de tinta na lata para evitar a flutuação da viscosidade causada pela dosagem de grandes quantidades de solvente com períodos relativamente grandes. Grande quantidade de tinta causa estabilização da viscosidade. No caso do RPS, doses de até 10 g são dosadas. Para poder bombear a tinta através do sistema, precisamos de pelo menos 4 kg de tinta e às vezes só temos 4.5 kg de tinta residual, enquanto a viscosidade se mantém estável o tempo todo porque quantidades muito pequenas são dosadas. Isso significa que menos tinta deve ser preparada para um pedido e menos tinta residual é criada. Isso também torna o RPS único, mantendo pequenas quantidades de tinta em uma viscosidade constante.
No caso de controles de viscosidade calibrados manualmente, os operadores frequentemente estarão inclinados a usar um cilindro anilox diferente com um volume diferente ou usando verniz para influenciar a força da cor, resultando em tempos de configuração mais longos.
Isso garante que realmente tenhamos alcançado um tipo de padronização de impressão de cores nos diferentes substratos. Isso economiza muito tempo. Com sistemas calibrados manualmente, isso é difícil de fazer. Qualquer operador precisa ter disciplina para calibrar os sensores antes da configuração da prensa e geralmente não tem tempo para fazer isso.
- Na sua opinião, o RPS entrega alguma proposta diferenciada para as gráficas? Você acha que Rheonics será capaz de causar impacto na indústria de impressão flexográfica com o RPS?
Resposta:
Em primeiro lugar, é o único sensor que foi calibrado pelo fornecedor e nunca mais precisa ser calibrado. Com este sensor é possível armazenar valores de viscosidade, possibilitando a automação. A variável mais importante é medida com sensores que não precisam ser calibrados manualmente para cada ponto de ajuste, o que elimina erros causados pelo operador.
Uma boa comparação entre Rheonics sensores com sensores disponíveis no mercado é um medidor de distância a laser e determina a profundidade de um poço deixando cair uma pedra e medindo o tempo que leva para atingir o fundo. Com pedra e relógio, o poço tem profundidade de 21,3 segundos, caso o poço não seja profundo o suficiente o cara com relógio diz “cavar mais 0,5 segundos” ou no caso de Rheonics, cave com precisão de alguns mm.
Se falo com o vendedor/técnico da tinta e há problemas com um cliente, é quase sempre porque a viscosidade da tinta é muito viscosa. Mesmo com colegas quando um erro é detectado durante a impressão, geralmente é que muito solvente é dosado na tinta, o que diminui a cororing força.
Uma das razões pelas quais todos aceitam que a viscosidade é expressa em segundos é que não havia sensores “confiáveis e reproduzíveis” medindo na unidade correta, então não havia alternativa.
Acredito que o sistema RPS eleva os padrões de segurança e as possibilidades de automação dentro da impressora e estabelece uma nova referência para as empresas de impressão em termos de qualidade, rentabilidade, precisão e exatidão de cores, gestão do consumo de tinta e solvente, conhecimento e controle dos operadores e impacto ambiental. Tenho certeza de que isso deixará uma marca na indústria de impressão flexográfica, pois traz a variável de impressão mais crucial, ou seja, a viscosidade da tinta, para as pontas dos dedos das impressoras. Rheonics Os sistemas de sensores RPS e SRV trazem as seguintes vantagens significativas e propostas exclusivas:
Vantagens técnicas: Automação de prensa, controle de qualidade, eficiência, precisão e meio ambiente
- Controle muito mais rígido e preciso (em 10-15 vezes, pelo menos) na qualidade da tinta quando comparado com outros sistemas equivalentes no mercado.
- Tempo de configuração mais rápido e densidade de cor precisa - auxiliado pela experiência e repetibilidade do sensor, carrega funções de configuração de trabalho do software
- Viscosidade compensada por temperatura: menor preocupação com variações sazonais, ou qualquer fator que possa afetar a temperatura (e portanto a viscosidade)
- Compensação por evaporação: controle rígido e 'resolução fina' da adição de solvente em pequenas etapas - tudo levando à economia de solvente e tinta
- Reduz o tempo de configuração e o desperdício de configuração - os operadores podem executar novamente um trabalho carregado anteriormente usando as funcionalidades 'Salvar trabalho' e 'Carregar trabalho', o que reduz o desperdício
- Análise de falhas e solução de problemas eficazes - a maioria dos problemas de impressão relacionados à cor e qualidade são atribuídos aos problemas de viscosidade. Os dados dos sensores e do sistema RPS garantem detecção de falhas eficiente, análise abrangente da causa raiz e ações corretivas eficazes de uma forma simples e intuitiva.
- Emissões reduzidas de solventes e resíduos e desperdícios reduzidos em comparação com o manuseio e configurações manuais.
- Redução no tempo de secagem e economia com a necessidade reduzida de recuperação de solvente devido ao uso ideal de solvente na tinta.
Instalação e usabilidade
- Tamanho compacto: pegada pequena na impressora, não afetado pelo ambiente - vibrações, etc. Outros sistemas semelhantes precisam de um esforço de instalação significativo e pegada dentro da impressora. Só precisávamos instalar o sensor diretamente na mangueira de tinta, usando um Tee de ¾ ”pronto para uso.
- O software é intuitivo, fácil de usar e valioso. Além disso, é útil para auxiliar o conhecimento dos operadores sobre as correlações de viscosidade e intensidade da cor - eles agora têm uma maneira inteligente de entender, experimentar para aprimorar o conhecimento sobre o comportamento das tintas - útil em trabalhos atuais e futuros. O software é feito em colaboração com os operadores, o que resultou em uma interface muito amigável. De vez em quando, um operador quer ver como a viscosidade se comportou durante a produção de um pedido, quão estável ela estava.
Rentabilidade
- Economia no consumo de solvente e tinta (também manutenção de registro do consumo de solvente): Controle mais rígido leva a menor consumo de solvente e tinta devido ao algoritmo inovador + superioridade do sistema.
- Tempos de configuração reduzidos levam ao aprimoramento da produtividade e à capacidade de concluir mais trabalhos de impressão ao mesmo tempo.
- Capacidade de realizar trabalhos de maior qualidade e maior margem (dE <2), aumentando a lucratividade e proporcionando uma vantagem competitiva
Algumas imagens do sistema RPS InkSight
- Rheonics Console SmartView integrado em máquinas de impressão
- Algumas fotos mostrando a instalação em linha dos viscosímetros SRV dentro da impressora
- Gabinete de controle autônomo
Todos os produtos da Rheonics são projetados para resistir aos ambientes mais severos, como alta temperatura, alto nível de impacto, vibrações, abrasivos e produtos químicos.
Artigos Relacionados
A Revista FTA Flexo apresenta uma Rheonics estudo de caso de usuário – “Padronização de viscosidade: abordagem de uma impressora”
Revista focada em impressão flexográfica - Flexo (https://www.flexography.org/flexo-magazine/) publica um artigo detalhado apresentando o Rheonics Viscosímetros SRV e a solução RPS InkSight Multi-Station Ink Control em um cliente na Holanda. Encontre o link para a publicação.
Padronização da viscosidade na impressão flexográfica
Na história da nossa empresa aplicamos todo tipo de sensor de viscosidade: rotacional, queda de bola, queda de pistão e onda acústica. A semelhança entre esses sensores é que todos são calibrados com um copo, no nosso caso o copo DIN com saída de 4 mm. Por si só isso funcionou bem e devido à falta de uma alternativa melhor ...